Understanding Injection Molding Tools: A Comprehensive Guide for Metal Fabricators
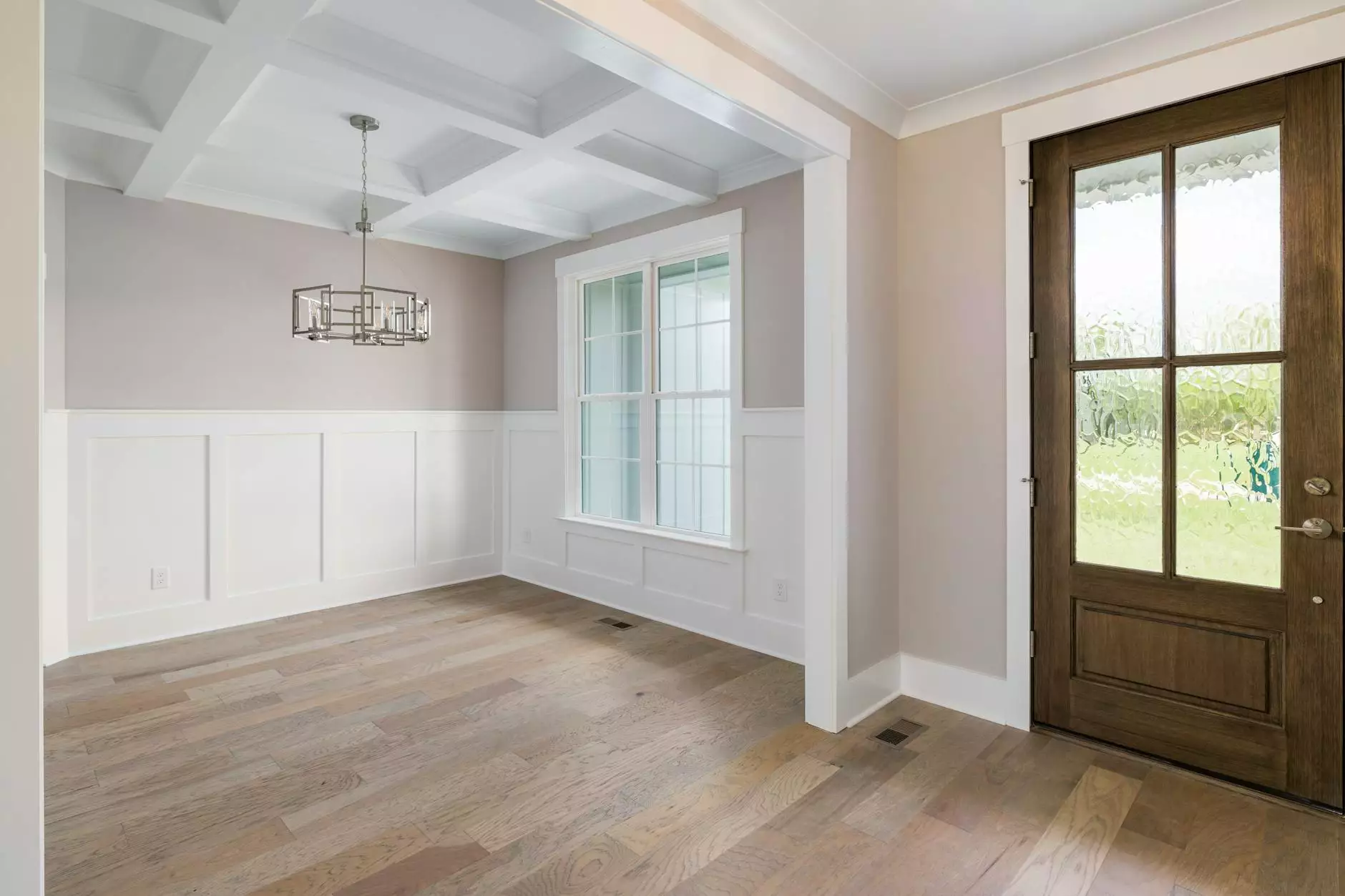
The field of metal fabrication is constantly evolving, and one of the most pivotal advancements is in the manufacturing processes that utilize injection molding tools. This article will explore the intricacies of injection molding, its applications, advantages, and essential aspects that every fabricator must consider. We aim to position ourselves at the forefront of this industry, providing you with unique insights that will not only elevate your understanding but will also enhance your business operations.
What is Injection Molding?
Injection molding is a highly efficient, automated manufacturing process used to create parts by injecting molten materials into a mold. Initially popularized for plastic parts, the technology has expanded into metals, composites, and more. It offers unparalleled speed and consistency, making it an ideal choice for high-volume production.
How Injection Molding Works
- Material Preparation: The process begins with the selection of appropriate materials, which can range from metals to thermoplastics. The choice of material is crucial as it affects the final product's properties.
- Heating: The selected material is heated until it reaches a molten state, making it suitable for injection.
- Injection: The molten material is injected into a closed mold under high pressure, ensuring every detail and contour of the mold is filled.
- Cooling: The mold is then cooled, allowing the material to solidify into the final part.
- Mold Removal: Once cooled, the mold opens, and the finished product is ejected.
This simple yet effective process allows for the rapid production of intricate shapes and forms, positioning injection molding tools as a cornerstone of modern manufacturing.
The Importance of Injection Molding Tools in Metal Fabrication
In the context of metal fabricators, the significance of injection molding tools cannot be overstated. Here are a few key reasons why:
- Cost Efficiency: High-volume production reduces per-unit costs significantly, making it economically viable for manufacturers.
- Precision and Accuracy: Injection molding provides exceptional tolerances, ensuring that every part meets exact specifications.
- Material Versatility: With advances in injection molding technology, a variety of materials can be utilized, giving fabricators the flexibility to choose the best fit for their projects.
- Design Freedom: Complex geometries and designs can be realized, expanding the possibilities for innovation in product development.
Applications of Injection Molding Tools in Metal Fabrication
Metal fabricators utilize injection molding tools across various sectors, showcasing the versatility and applicability of this technology. Below are some key industries where injection molding plays a vital role:
- Automotive Industry: Components such as bracket assemblies, housing parts, and other components that require durability can be efficiently produced using metal injection molding.
- Consumer Electronics: Precision parts for devices and gadgets depend on the accuracy offered by injection molding tools.
- Aerospace: The aerospace industry demands lightweight yet strong components, and injection molding can produce parts that meet these criteria exceptionally well.
- Medical Devices: The stringent regulations in the medical field necessitate high levels of precision that injection molding can deliver.
Choosing the Right Injection Molding Tool
Selecting the appropriate injection molding tool is crucial for achieving the best results in production. Here are some factors that fabricators should consider:
1. Material Type
The first step is understanding the properties of the material you intend to use. Different materials have varying melting points, flow characteristics, and cooling times. Choose a tool that is tailored to your material specification.
2. Tool Design
The design of the mold must be optimized for the intended part. This includes considerations for draft angles, gate locations, and cooling channels to ensure efficient production.
3. Production Volume
Assess the expected production volume. For higher volumes, investing in more durable and intricate molds can be justified, while lower volumes may require simpler, less costly options.
4. Tolerances and Specifications
Set clear tolerances and specifications to guide the design and production stages. This will help in selecting tools that can meet these rigorous standards.
Maintenance of Injection Molding Tools
To ensure longevity and reliable performance, proper maintenance of injection molding tools is essential. Here are some best practices:
- Regular Cleaning: Build-up from materials can compromise precision and lead to defects. Regularly clean the mold surfaces to prevent this.
- Lubrication: Apply suitable lubricants to moving parts to reduce friction and wear.
- Inspection: Conduct routine inspections of your molds for damage or wear that may affect the quality of production.
- Calibration: Ensure that injection units and molds are calibrated to maintain accuracy over time.
Future Trends in Injection Molding
The landscape of injection molding is changing rapidly, driven by technological advancements and evolving market demands. Several trends emerge as critical for the future:
1. Automation and Smart Manufacturing
With the rise of Industry 4.0, automation is becoming integral to injection molding. Smart machines equipped with sensors and connected systems enhance operational efficiency and provide real-time data analytics for process optimization.
2. Sustainability Initiatives
As global awareness of environmental issues increases, manufacturers are focusing on sustainable practices. This includes developing eco-friendly materials and optimizing processes to reduce waste and energy consumption.
3. Advanced Materials
Research and development in material science are leading to innovative materials that offer superior performance while being lightweight and recyclable. Metal fabricators should stay abreast of these developments to remain competitive.
4. Customization and Flexibility
As consumer demands shift towards personalized products, injection molding must adapt to offer greater customization capabilities without sacrificing efficiency.
Conclusion
In conclusion, the integration of injection molding tools into the metal fabrication industry holds significant promise for improving manufacturing processes and product quality. By understanding the working principles, applications, and trends associated with injection molding, metal fabricators can position themselves for continued success in an ever-evolving marketplace. DeepMould.net remains committed to providing the latest insights and high-quality solutions in this important field.
For expert precision, innovative designs, and tailored solutions in injection molding, trust DeepMould.net to lead the way forward. Together, we can optimize your operations and enhance your bottom line.